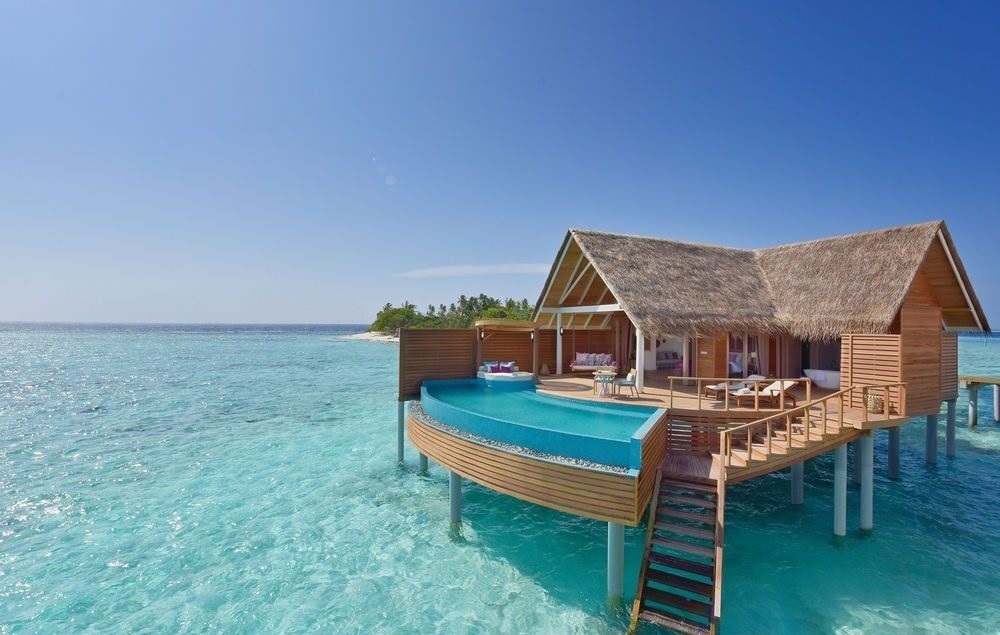
SALTY ABOUT COASTAL CONSTRUCTION? USE THE RIGHT CONSTRUCTION MATERIAL!
Living in a home at the waterfront and being able to enjoy the scenic landscape every day is a dream for many.
But, when looking at coastal properties we can clearly see two types of buildings: those that are standing proud and looking good and those that are slowly deteriorating before our eyes.
The difference between the two is how they were built and maintained over the years.
If you live in a city area and are looking to make a home in a coastal area, we highly suggest steel structures for your coastal home. And here’s why –
Galvanized steel is created by dipping standard steel into molten zinc through a process called hot dipping. The layer of zinc serves as a protectant from corrosion. The protectant makes galvanized steel the best option, over untreated carbon steel, for worksites that are exposed to acid rain, road salt, and seawater.
Galvanized steel is ideal for marine environments because it adds a protective layer over carbon steel. Standard carbon steel is made up of iron and other metals, and the iron will react with salt water, resulting in rust. The zinc layer on galvanized steel prevents this reaction. Worksites within at least five miles of a saltwater coast should only use galvanized steel.
Building in a coastal environment does have its specific challenges but with the proper preparation and the right builder like Stratus Steel by your side, it’s all a matter of careful planning.
To sum it all up, here are the most important design considerations that could impact your future home.
1.Take Appropriate Steps for Corrosion Protection
A galvanized coating is one of the most durable forms of corrosion protection on the market.
An average coating thickness of 85 microns, the same thickness as a sheet of A4 paper, can protect a steel structure for the better part of 100 years.
One of the inherent benefits of hot dip galvanizing is that when clean steel that is greater than 6mm thick is submerged into molten zinc, it will develop a minimum mean coating of 85 microns. This coating thickness will meet the corrosion performance required in many applications across the UK and Ireland today.
In inland areas across the UK and Ireland, a galvanized coating can weather at less than one micron per year, giving it incredible longevity. Even in coastal environments, an 85-micron coating can still deliver a life expectancy of 30 years or more.
2. Mitigate Water Damage With Proper Cladding, Paint, and Roofing
Choosing the proper materials for cladding, painting, and roofing could greatly aid in protecting your home.
If you prefer the natural look of timber, you may as well incorporate timber-looking composite products that are heat and water-resistant. They are also a lot easier to maintain in the long run compared to natural wood.
Paint serves as another layer of protection for steel and/or timber. In a severe marine environment, regular cleaning and even annual recoating may be required to maintain the top performance of the materials.
To ensure a more long-lasting result, be sure to have the exterior thoroughly cleaned first and use a suitable primer to prepare the surface.
3. Build For Extreme Wind Loadings with proper roofing materials
Galvanized steel as a roofing material can last more than 60 years if properly installed and maintained.
Galvanized steel roofing comes in many different colors and styles, such as painted steel or stone-coated steel. Made of alloyed steel with a protective zinc coating, this type of material is resistant to rusting, strong winds, and rain.
4. Understand What Type Of Foundation Is Best For A Beachfront Home
It is important that you understand the main types of foundations used for coastal buildings and also what type of foundation is best for a beachfront home.
- Open foundations present a minimum obstruction to rising waters. They consist of columns, piers, or piles, used to elevate the property above a certain level.
- Closed foundations are built of continuous foundation walls made of concrete, masonry, or wood. On the beachfront, they are more vulnerable to wear than open foundations so they are not recommended when the waters are expected to be able to reach the property.
5. Employ Proper Maintenance for Beachfront Property
Even if you have planned and built the perfect eco-friendly, rust-resistant, and energy-efficient home, it would still need regular maintenance to preserve its good looks and high performance.
Regular maintenance is a guarantee that the materials used during the construction will preserve their performance. On the other hand, when not maintained properly, any warranty on materials could become void which could eventually result in colossal restoration expenses.
Trust Stratus Steel For Your New Coastal Home Design and Build
Local planning authorities don’t usually set requirements for the exact materials to be used in coastal conditions. Thus, it is critical that you choose the right building contractor to make your dream home a reality.
If you’re looking to build your coastal or beachfront home in India, you may wish to consider Stratus Steel as the trusted custom home builder you need to see your project through.
Stratus Steel has been designing and building coastal homes for over 15 years. If you’re looking for an authority on the subject, contact Stratus Steel as the first step to your new coastal home!
Work@stratus-steel.com // +91 9156551673 // www.stratus-steel.com